Built to Last: General Rules of Thumb for Estimating the Useful Life of your Building Envelope
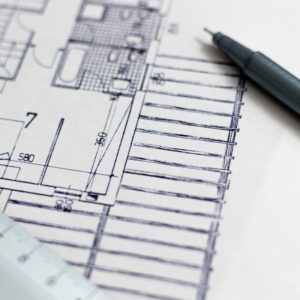
By: Erin Collins-Cecil, Assoc. AIA, Project Consultant/Architectural Designer
Common perception used to be that older homes were “built to last;” quality craftsmanship and building materials were the norm. However, that perception has changed to “everything is disposable.” Has the quality of construction and materials declined over time?
Technology, new manufacturing processes, and improved transportation infrastructure have resulted in a greater variety and availability of building materials. Although there are still trade specialists such as brick masons who can be considered experts in their field, many construction workers have not been educated as to proper installation practices of these new materials, nor how they integrate with the work of other trades. In addition to proper installation, other factors that will affect the longevity of building materials are geographical factors and the microclimate of the site. Further, once installed, most building materials and systems require periodic maintenance to achieve maximum performance. For example, brick exterior walls will require mortar joint re-pointing, and stucco systems could benefit from hairline crack repairs.
Roofing, cladding materials, windows, and doors which together comprise your building’s exterior “envelope,” have an estimated “normal economic life.” Miller+Dodson Associates, Inc., Capital Reserve Consultants, defines the normal economic life as “The number of years that a new and properly installed item should be expected to remain in place.” The normal economic life of a building material should be listed in your building’s capital reserve study.
In the absence of a capital reserve study, the average life expectancy for components of a building enclosure can be estimated as follows:
Roofing Materials
- Asphalt Shingles 20-30 years
- Copper or Metal Roofs 40-70 years
- Copper Gutters 50 years
- Copper Downspouts 100 years
- Aluminum Gutters 25 years
- Low Slope Membrane:
- TPO (PVC) 10-20 years
- EPDM (Rubber) 15-25 years
- Modified Bitumen 20 years
- Slate Shingles 60-150 years
- Steel Gutters & Downspouts 20 years
Cladding Materials
- Manufactured Stone Veneer 50 years, with maintenance every 10 years
- Aluminum Siding 25-40 years
- Brick Cavity Wall 50-100 years
- EIFS 20-50 years
- Fiber Cement Board 45-100 years
- Stucco 30-50 years, with repairs and maintenance every 10 years
- Vinyl Siding 25-60 years
- Wood Siding 20 years
Balconies and Decks
- Composite planks 8-25 years
- Structural wood members 10-30 years
- Vinyl Balcony Membranes 10 years
- Wood planks 15 years
Windows
- Aluminum or Clad 15-30 years
- Skylights 10-20 years
- Vinyl 20-45 years
- Wood 30 years
The estimated economic life of building materials can vary greatly! As indicated, the difference in expected useful life varies with the quality of the materials, craftsmanship, normal and routine maintenance, along with geographical factors and the microclimate of the site.
Most building envelope components have a manufacturer’s warranty, or guarantee, for a certain period of performance, however, because warranties are not intended to cover a building material for its full normal economic life, warranties will differ from the typical useful life listed above. If you suspect that a roofing or cladding material is not performing as intended, it is best to first check the material warranty. Most roofing and cladding materials have a warranty that covers only the material if it is installed according to manufacturer recommendations. In some cases, typically for stucco, EIFS, and low-slope membrane roofing systems, a warranty will only be provided if it is either installed by a certified contractor, or a manufacturer representative has inspected the installation of the material and believes it to be correct per the manufacture’s details. If a material is covered under warranty, the manufacturer will likely send a representative to your site to determine if the material itself is prematurely failing, or it the failure is a function of improper installation, and make recommendations on how to remediate the issue.
In most cases, a building professional, such as an Architect or Engineer, should be consulted to evaluate the roofing or cladding material, and determine if replacement is necessary. The building professional can develop drawings and specifications for the installation of new materials, which should incorporate flashing and weather barriers, required to meet building code requirements and to promote the longevity of the individual materials and the building as a whole.
All building envelope materials will need to periodically be replaced or repaired and maintained. If installed properly and coordinated with appropriate weather barriers and flashing materials, the building envelope can be considered to be “built to last.”
References:
- https://www.nachi.org/life-expectancy.htm
- http://millerdodson.com/
- Fannie Mae, Instructions for Performing a Multifamily Property Condition Assessment (Version 2.0), Appendix F Estimated Useful Life Tables, form 4099F, 2014 https://www.fanniemae.com/content/guide_form/4099f.pdf
One Response to “Built to Last: General Rules of Thumb for Estimating the Useful Life of your Building Envelope”
Leave a Reply
It is very interesting to me that slate shingles actually do last a lifetime. My wife and I might need to do an architectural property condition assessment. That way we know how much life we have left in our house.